Let’s Dispel Some Common Misconceptions About Fluid Analysis
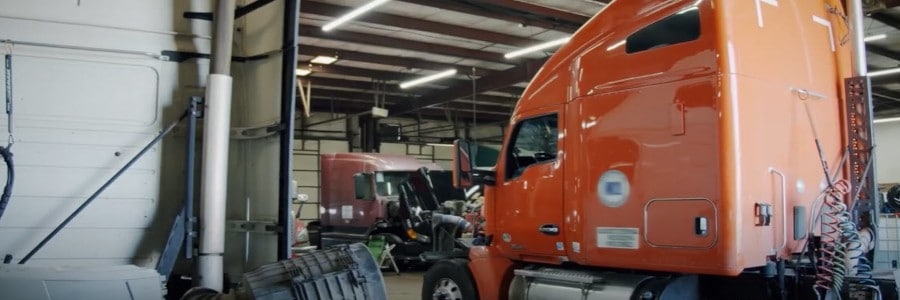
At Chevron, we are strong advocates of regularly scheduled, in-service fluid analysis for both on-highway and off-highway equipment. We have seen first-hand how it can help fleets identify potential issues to avoid costly unscheduled equipment repairs and downtime. Yet we still hear some skepticism about the value of fluid analysis from fleet operators who question whether it’s worth the time, effort and expense. So, let’s look at some of the common misconceptions about fluid analysis, as well as the benefits of a systematic well executed fluid analysis program.
Why not just change the oil? The equipment is scheduled for maintenance anyway.
If you’re having a problem with the equipment, changing the oil may correct it. However, fluid analysis tells you much more than just the condition of the oil. It tells you if you are experiencing a coolant leak, dirt ingestion, or fuel dilution for example, in the oil. If the viscosity is increasing, that could be an indicator that your equipment is overheating, oxidizing the oil, or reducing your fuel economy. Wear metals in the oil analysis may mean a part is generating wear or that dirt ingestion is causing abrasion. Just changing the oil won’t solve any of those problems, and might make matters worse by hiding the problem until it reappears as an unexpected failure.
Think about how much a doctor can tell you about your physical health just by taking a small blood sample. Fluid analysis does the same for your equipment.
Pulling samples is a pain. Who has the time?
It’s simply a matter of establishing a routine fluid analysis program and making it part of your preventative, predictive and proactive maintenance program. Establishing the sampling procedure is part of this program. A variety of options exist to best fit your equipment. Many pieces of equipment are equipped with push-button sampling valves or other sampling valves, and while utilizing sampling valves is the simplest and cleanest way to take a sample, another way is to use what we call a “vampire” sampling pump. This sampling tool extracts the fluid from the compartment through a tube attached to a sampling bottle. Your fluid analysis lab can provide the necessary sampling tools for you.
Some people take the sample at the time of the oil change, from the drain plug, but that can be messy and inconsistent. Ideally, a sample can be taken mid-drain, but mid-drain may be defined differently from one technician to the next. A sample taken too early or too late may capture more contaminants, creating erroneous or ‘ghost’ wear metals in the data analysis.
The report is confusing and hard to understand.
The lab will work with you to explain the report. The laboratory will flag any wear metals, contaminants or physical properties that need monitoring or any immediate corrective action which will be addressed in the laboratory’s diagnostic comments. After your first few reports, you will most likely be comfortable with the process and learn to read the reports with minimum guidance. The fluid analysis laboratories or your lubricant’s representative are always there to answer any questions.
Just follow the OEM’s directions on the type of oil and frequency of drains, and you shouldn’t need an oil analysis.
To repeat: it’s not just about the condition of the oil, it’s about the health of the equipment. Most OEMs work with the fluid analysis labs to provide optimal limits or statistical analysis is used to enhance the data interpretation. Which is why it’s critical to provide a complete equipment list, along with all of the make and model information, to the lab. Also, a key component in diagnosing samples is properly providing mileage/hours of service for each sample because this piece of information can completely change the data analysis interpretation.
Fluid analysis is a business management tool. Equipment owners are holding onto their equipment longer and trying to maximize their useful life. Fluid analysis can help you make better buying and selling decisions by showing you which equipment is performing better, which is costing more to maintain, and which may be headed for failure. Most importantly, it sets the stage to be preventative, predictive and proactive to reduce the cost of unpredictable downtime. You can also use it to support a warranty claim and show that you have been keeping up with the maintenance. If you’re in the market to buy a used piece of equipment, you can take an oil sample from it and get a report back on the health of the equipment typically within 24 to 48 hours. You can also utilize the sampling history when you trade or sell your equipment to perhaps increase potential resell value.
Fluid analysis is expensive.
If you use a program like Chevron’s LubeWatch Program, which provides services to multiple on- and off-highway equipment companies, you can benefit from economies of scale and efficiency. Oil analysis is not a one-time test, it’s something you want to do consistently, following the same procedures and using the same lab, so you can see trends and patterns over time. Your labor and equipment costs should decline as the process becomes more routine.
Think of oil analysis as an insurance policy. Yes, you must pay a premium, but you’ll pay a lot more when a piece of equipment breaks down unexpectedly. We have also seen that equipment companies that have a regular oil analysis program are more conscientious about preventive maintenance. If you’re willing to take the time and effort to pull samples and follow up on the lab reports, you will recover the nominal cost of fluid analysis by minimizing costly maintenance and unscheduled downtime.